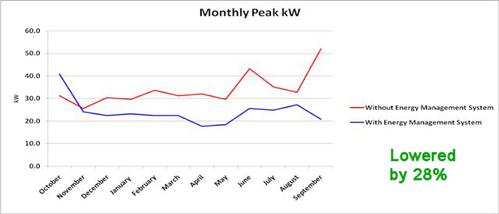
Written by Jeff Vernon, Envirotrols Group
Knowledge is power. Knowledge also saves power.
It makes sense that monitoring your energy consumption will enable you to have more control over the amount you spend for energy. Doing this effectively, however, is not as simple as it sounds. The electric company typically provides a lump sum bill at the end of the month. If the current monthly total is higher than the previous month the cause is often not obvious. Was the increase due to weather, a short-term glitch, or a prolonged pattern of neglecting to pay attention to usage patterns? It is difficult enough to get control of your energy usage when you’re right on top of it, but the problem is even tougher for businesses that manage remote facilities, thousands of miles apart. Among the industries grappling with the issue of large energy bills are self-storage companies who manage large volumes of climate controlled space. Most often they have a network of large capacity buildings throughout the country where a significant amount of energy consumption occurs, and a single corporate office which sets energy use policies and pays the bills. Continuous monitoring and control is required for personnel at the home office to know whether energy use directives are being complied with at each site. For example, a corporate standard may dictate what temperatures should be maintained at a facility, but often the thermostats aren’t locked and customers and employees can freely change the temperature settings. People also forget to turn lights off when they leave. The amount of wasted energy depends on the level of attention each store and/or district manager is giving to the situation, but on-site store managers may understandably be more concerned with activities directly tied to increasing number of units rented and other revenue generating activities. Energy monitoring and control system providers are sensitive to this problem, and apply their knowledge of automation technologies to implement control strategies that consistently save businesses as much as 30-35% on their energy bills. The savings are realized quickly enough to achieve a 6-month to two-year ROI when an energy management and control system is installed. Let’s take Safeguard Self Storage, Inc. of Atlanta, Georgia as a case in point. Corporate facilities management personnel in Atlanta are responsible for managing the company’s 60+ locations nationwide. About three years ago, headquarters suspected that money was being wasted on excessive energy use at Safeguard’s Bronx, New York facility. At that time, energy for this facility was costing Safeguard approximately $55,000 per year. Safeguard contracted with a supplier and integrator of environmental control systems to perform a study of the energy consumption patterns at the Bronx site. The integrator found that the thermostat at the facility was being maintained at 72º throughout the year, despite a corporate standard of 78º in summer and 55º in winter. Even more excessive cooling or heating was occurring because the thermostats had lockboxes that weren’t locked and anyone could change the settings at will. In addition, the inspector found that the outside lights were on continuously because time clock settings were removed. Facility energy costs can be reduced significantly by shutting off unnecessary lighting outside of operating hours, although this is not always desirable for security reasons. As a result of the findings in the report, Safeguard asked the integrator to help them bring energy costs under control at the Bronx facility. Technicians removed the building’s thermostats and light switches and installed a central building management system. The system provides automated lighting and climate control for the Bronx facility consistent with Safeguard’s corporate energy use policies. The building management system is configured to meet specific customer needs. For example, Envirotrols technicians enter a peak demand (peak kW) target specific to each facility. The control system continuously monitors electrical loads and forecasts peak demand that will occur in the local utility’s time window, normally a 15 or 30 minute timespan that the utility uses for computing excess energy consumption. If demand spikes for a few minutes the system can automatically adjust building temperature setpoints, implement duty cycling, and initiate other load shedding measures designed to cut demand and keep the facility under its target. After the high demand event occurs, the system resumes normal operation. The control system integrator works with the on-site store manager and corporate office to plan the order in which systems will get adjusted, and the extent to which output is reduced or turned off, to minimize any negative impacts on normal business operations, and then configures the system to implement those pre-planned control strategies in the event of a demand spike. Facility space conditioning requirements and energy cost tolerances can be based on many factors, so being configurable to meet specific facility requirements is a key requirement for the building control system. For example, in multi-floor storage buildings, the top floors typically have the most heat load so the system is configured to shed cooling equipment loads on the core and lower floors first. The control system relies on a PowerScout power meter for accurate, continuous monitoring of loads in the facility. For ease of installation, the system uses RoCoil Rogowski-style current transformers (CTs), and easy Modbus integration to the central control system. The flexible “rope” style sensor coils are installed around the electrical service lines going to the lighting and HVAC equipment. Their flexibility makes them easier and faster to install in most cases than current sensors that employ rigid clamps. The CTs that were selected also support a 50-5000 Amp range so one set of CTs can provide accurate data whether the facility is at peak demand or is fully turned down. The energy management and control system is securely accessible on the web, so Safeguard’s energy managers in Atlanta can safely and conveniently view real-time energy consumption of any location in their network at any time. The building control system also produces automated notifications when it detects problem conditions occurring. Local and regional managers use a web browser to view the status of any facility that reports to them, but only on-site managers are granted the authority to override the control system and allow a facility to deviate from corporate energy use guidelines when the need is justified. (see Figures 3a- 3c). Engineers at the building control system integrator’s home facility monitor their customers’ energy consumption, too. They can tell their customers when a problem load comes on because the PowerScout meter helps them instantaneously know when a problem has occurred. But, the real payoff is in analyzing the data. The integrator sets up the control system so that the Safeguard IT people are able to develop their own reports. The controls are also designed to protect against tampering with temperatures at the site. For example, if someone puts a heat lamp on a sensor at a remote storage site to try and activate the air conditioning system an alarm event is triggered and an email is sent to corporate headquarters. The alarms also appear on the system’s web monitoring screens. To make it easier to compare the levels of energy usage over time, the reports are normalized based on historical temperature data, factoring out the effects of different weather patterns year over year. To help storage companies compare facility performance across their network the reports are able to display energy usage on a square foot basis. With the installation of the new control and monitoring system Safeguard cut the energy demand charge component of the monthly power bill by two thirds, and achieved a nine- to twenty-four month return on their energy cost management system investment. “By focusing on demand control, we are reducing our carbon footprint, lowering our operating costs, and improving our margins. Also, by monitoring our HVAC units, we were able to reduce our maintenance cost by 28% with a savings of $44,000,” said Mike Frosaker, VP of Asset Management for Safeguard Self Storage. Figure 4 compares monthly peak power consumption at the Safeguard Bronx facility before and after the energy management system. Since the Bronx pilot project, the monitoring and control system installation has been repeated at 61 other Safeguard facilities with similar positive results. For example the Oak Lane, Philadelphia facility, the second Safeguard facility to be automated, saved $20,000 in energy costs the first year after an initial investment of $14,000. Personnel at the control system integrator’s office monitor every installed system for 6 months and guide the customers as to how to utilize the information to diagnose problems and save energy costs. When they find things worthy of noting, they do a screen capture of the graphs and send explanations to their customers. They can also look at customers’ power bills and, when they see anomalies or trends, investigate why this is occurring. The system integrator can tell their customers exactly what the extra power is costing them while verifying that the customer is on track to achieve the ROI target. ♦ Download a PDF copy of this story here.